Definición de plan de mantenimiento óptimo para equipos críticos de una planta de laminación
Tesis
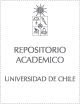
Publication date
2015Metadata
Show full item record
Cómo citar
Meruane Naranjo, Viviana
Cómo citar
Definición de plan de mantenimiento óptimo para equipos críticos de una planta de laminación
Professor Advisor
Abstract
El objetivo del presente trabajo de título es la definición de un plan óptimo de mantenimiento para los equipos críticos de una planta de laminación de metales.
En la actualidad, las empresas están invirtiendo en la definiciones de planes de mantenimiento acotados a su realidad, lo que permite sacar el mayor provecho a sus equipos y, con ello, minimizar costos asociados a ceses de producción, costos en compra y almacenamiento de repuestos y costos en horas hombre de reparación, entre otros. Un buen plan de mantenimiento constituye un gran aporte a cualquier proceso productivo.
La primera etapa del plan es el análisis de falla y criticidad de los equipos. Una vez definidos los equipos o componentes críticos se puede proceder al estudio de costos asociados. Existe una gran cantidad de modelos para el estudio de los costos, la selección del más apropiado depende del caso en estudio. Por último, es necesario definir una estrategia de mantenimiento y una frecuencia óptima de inspecciones.
Luego de realizado el estudio, se definió un plan de mantenimiento preventivo para todos los equipos críticos analizados, con excepción del sistema de lubricación del Tren Medio. Sin embargo, no es posible generar un plan detallado debido a la falta de datos precisos para los componentes de cada equipo. Por esta razón, en primer lugar se generó un análisis de sensibilidad para esclarecer cuál es el horizonte de aplicación de los planes de mantenimiento definidos (según los costos utilizados). Además, se ha estudiado la frecuencia óptima de inspección para cada equipo. Cada inspección considerando que la detención del equipo no es necesaria. Es decir, inspecciones visuales, auditivas o en base a sensores que no impliquen un gran costo o la detención del equipo.
En definitiva, los resultados obtenidos para cada equipo son los siguientes:
- Ventilador aire combustión: Mantenimiento preventivo cada 15 días / 6 inspecciones preventivas mensuales.
- Sistema Kick-Off: Mantenimiento preventivo cada 68 días / 4 inspecciones preventivas mensuales.
- Lubricación Tren de Desbaste: Mantenimiento preventivo cada 85 días / 4 inspecciones preventivas mensuales.
- Lubricación Tren Medio: Mantenimiento correctivo / 6 inspecciones preventivas mensuales.
- Motor del Monoblock: Mantenimiento preventivo cada 29 días / 11 inspecciones preventivas mensuales.
- Sistema Neumático: Mantenimiento preventivo cada 106 días / Inspección preventiva mensual.
Por otra parte, se estima que existirá un 25% de ahorro en el costo total de mantenimiento para el total de equipos críticos estudiados en el presente documento.
General note
Ingeniero Civil Mecánico
Identifier
URI: https://repositorio.uchile.cl/handle/2250/132720
Collections
The following license files are associated with this item: