Case study: Discrete element modeling of wear in mining hoppers
Artículo
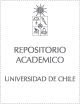
Open/ Download
Publication date
2019Metadata
Show full item record
Cómo citar
Rojas, Eduardo
Cómo citar
Case study: Discrete element modeling of wear in mining hoppers
Abstract
A discrete element method is designed to evaluate the relative wear on hoppers caused by friction during operation in an open-pit mine. The results of the model show good agreement with measurements on real industrial hoppers. Grains are modeled as triangular or tetrahedral clusters of particles that interact via dissipative contact forces. Also, the case of spherical particles is included for comparison. The wear is obtained using Archard's model, adapted for discrete element simulation, allowing the spatial distribution of wear on the bottom surface of the hopper to be obtained. It is found that the model is grain-shape sensitive, showing better agreement with measurements when using clusters compared with spheres. In general, the loading phase produces greater wear at the front of the hopper (near the cabin), while for the unloading phase, the maximum wear is in the rear zone. This combined effect agrees with in situ measurement on a mining hopper during its operation, especially when using tetrahedral clusters, revealing an error of less than 20% along the longitudinal wear curve. Clusters built from spheres can be successfully used to simulate the process in an accurate way and at low computational cost compared with more realistic rock shapes. The method can be used to model the wear distribution in hoppers and other facilities used in large scale industries.
Indexation
Artículo de publicación SCOPUS
Identifier
URI: https://repositorio.uchile.cl/handle/2250/172155
DOI: 10.1016/j.wear.2019.04.020
ISSN: 00431648
Quote Item
Wear, Volumen 430-431,
Collections